ASME Flange Design Calculation
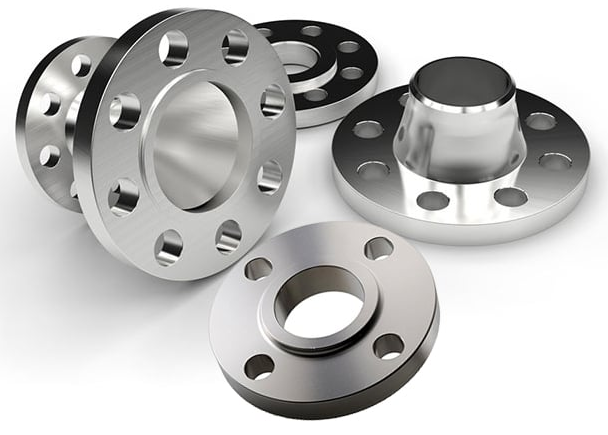
Description
Flange qualified for B31.3 service per 304.5.1(b) using ASME BPVC Section VIII Division 1 App.2. Alternatively flange may be qualified for B31.3 per 304.7.2(a) 'extensive successful service'. Items highlighted in Blue are information from drawing. Items highlighted in Orange are information estimated by engineer. Calculation checks: Flange Stresses, Bolting Criteria, Weld Criteria, Rigidity Criteria, Gasket Seating Condition Satisfied, MAWP based on Bolt Stress, MAWP based on Flange Stress and Total Permissible MAWP.
ASME B31.3 (Process Piping) provides guidelines for the design, fabrication, and installation of piping systems in process plants. Section 304 of ASME B31.3 covers the design rules for components such as flanges. According to ASME B31.3, a flange can be qualified for service in two ways:
- Per Section 304.5.1(b) - Using ASME BPVC Section VIII Division 1 Appendix 2:
If the flange is designed according to the rules specified in ASME Boiler and Pressure Vessel Code (BPVC) Section VIII Division 1 Appendix 2, it can be qualified for B31.3 service. Appendix 2 provides design rules for custom flanges and flanged fittings, which can be used to determine the thickness, bolt size, and gasket dimensions for the flange, considering the pressure-temperature rating and allowable stress values.
When designing a flange according to ASME BPVC Section VIII Division 1 Appendix 2, ensure that you adhere to the design rules, material specifications, and fabrication requirements as specified in the code. Once the flange is designed, fabricated, and inspected according to these rules, it can be considered qualified for B31.3 service.
- Per Section 304.7.2(a) - 'Extensive Successful Service':
Alternatively, a flange can be qualified for B31.3 service if it has been in extensive successful service under comparable conditions of pressure, temperature, and cyclic loading without any detrimental effects on its performance. This qualification is based on the historical performance and service life of the flange and can be considered if the flange has been consistently reliable in similar operating conditions.
To use the 'extensive successful service' qualification, you need to provide sufficient documentation and evidence of the flange's performance in similar operating conditions, such as maintenance records, inspection reports, and failure analysis data. The evidence should demonstrate that the flange has been consistently reliable and has met the required performance criteria without any significant issues or failures.
In summary, a flange can be qualified for B31.3 service either by designing it according to ASME BPVC Section VIII Division 1 Appendix 2 or by demonstrating its extensive successful service under comparable conditions. Both methods require adherence to the relevant codes, standards, and design rules, as well as proper documentation and evidence of the flange's performance and reliability.
Calculation Preview
Full download access to any calculation is available to users with a paid or awarded subscription (XLC Pro).
Subscriptions are free to contributors to the site, alternatively they can be purchased.
Click here for information on subscriptions.