Aerospace_lug_analysis.xls
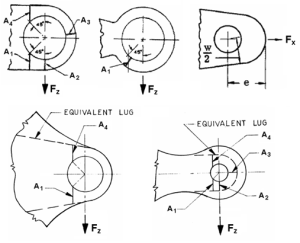
Description
This method of assessment involves reading coefficients from graphical data for use in subsequent equations. The spreadsheet automates all the curve reading to determine the proof and ultimate strength of lugs in an expedient manner.
The spreadsheet has been produced by Abbott Aerospace an independent consultancy company offering structural engineering services the aerospace industry. You can contact them by email
Calculation Reference
Bruhn - Analysis & Design of Flight Vehicle Structures
Currey - Aircraft Landing Gear Design
In classical engineering analysis, the assessment of lug strength involves considering the applied loads, geometry of the lug, and material properties to determine stresses and potential failure modes. Here's a step-by-step approach for the classical analysis of lug strength:
- Geometry and Loading Conditions:
- Define the geometry of the lug, including dimensions such as diameter, thickness, and fillet radii.
- Identify the applied loads, including axial forces, shear forces, and moments.
- Take into account any additional loading conditions, such as thermal effects or dynamic loads.
- Axial Stress:
- Calculate the axial stress using the applied axial force and the cross-sectional area of the lug.
- Ensure that the axial stress is within the allowable limits of the material.
- Shear Stress:
- Determine the shear stress caused by applied shear forces.
- Consider both direct shear stress and torsional shear stress, depending on the loading conditions.
- Verify that the shear stress is within the material's allowable limits.
- Bending Stress:
- If there are bending moments, calculate the bending stress using standard beam bending formulas.
- Check that the bending stress is within the material's allowable limits.
- Combined Stresses:
- Combine axial, shear, and bending stresses using appropriate stress combination methods (e.g., von Mises criterion).
- Compare the combined stress with the material's allowable stress to assess overall strength.
- Fillet Stresses:
- Consider the stress concentration at fillet radii, as abrupt changes in geometry can lead to localized stress concentrations.
- Calculate and assess the fillet stresses to ensure they are within acceptable limits.
- Safety Factors:
- Apply safety factors to account for uncertainties in material properties, loading conditions, and analysis assumptions.
- Ensure that the calculated stresses, with safety factors applied, are still within the safety margins.
- Failure Criteria:
- Evaluate the potential failure modes, such as yielding, buckling, or fracture.
- Use appropriate failure criteria based on the material properties and loading conditions.
- Optimization:
- Explore design modifications to optimize the lug for weight, cost, or other factors while maintaining safety.
- Documentation:
- Document the analysis methodology, assumptions, and results for future reference and verification.
Calculation Preview
Full download access to any calculation is available to users with a paid or awarded subscription (XLC Pro).
Subscriptions are free to contributors to the site, alternatively they can be purchased.
Click here for information on subscriptions.
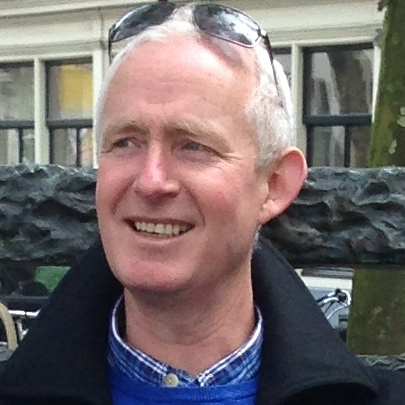