Aluminum Design Manual Welding
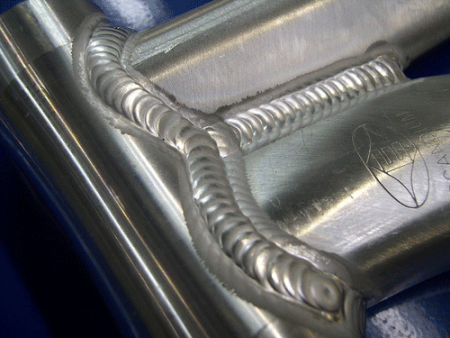
Description
Uses rules and properties from the Aluminum Design Manual to size different welds. Includes many types of aluminum base and weld metals.
Calculation Reference
Weld Design
Aluminium Welds
Strength of Welds
The Aluminum Design Manual (ADM) provides guidelines for designing and sizing welds for aluminum structures. The following are some basic rules and properties to consider when sizing welds for aluminum:
-
Weld type: The type of weld (e.g., fillet weld, groove weld) should be selected based on the application, load-bearing requirements, and geometry of the structure. Fillet welds are typically used for connecting plates or sections at right angles, while groove welds are used for butt joints, T-joints, and corner joints.
-
Material thickness: The thickness of the aluminum material being welded affects the required weld size. Thicker materials generally require larger weld sizes to ensure adequate strength and load-carrying capacity.
-
Weld strength: The Aluminum Design Manual provides minimum and maximum allowable weld strengths based on the material's alloy type and temper. The weld strength should be checked against the required strength for the specific application.
-
Weld size: The size of a weld refers to its throat thickness, which is the minimum distance from the root of the weld to its face. The throat thickness of a fillet weld is determined by multiplying the leg length (the distance from the root to the toe of the weld) by the sine of the included angle (usually 45 degrees for fillet welds). For groove welds, the throat thickness is equal to the depth of the weld's penetration.
-
Effective length of welds: The effective length of a weld refers to the length over which the weld is capable of transferring loads. The Aluminum Design Manual provides guidelines for calculating the effective length of welds based on the type of connection and loading conditions.
-
Weld spacing and edge distances: Adequate spacing between welds and edge distances (the distance from the edge of the material to the centerline of the weld) are essential to ensure proper stress distribution and avoid stress concentrations that can lead to weld failure. The Aluminum Design Manual provides minimum spacing and edge distance requirements based on the weld size and material thickness.
-
Weld quality and inspection: The quality of welds should be checked according to the guidelines provided in the Aluminum Design Manual, which includes visual inspection, non-destructive testing (NDT), and destructive testing methods as needed. Weld quality is critical to ensure the long-term performance and reliability of the welded structure.
-
Precautions for welding aluminum: Aluminum welding requires special considerations due to its material properties, such as its high thermal conductivity, sensitivity to heat, and susceptibility to oxide formation. Proper welding techniques and procedures, as outlined in the Aluminum Design Manual, should be followed to ensure strong and durable welds.
Always consult the Aluminum Design Manual for specific guidelines and requirements when designing and sizing welds for aluminum structures.
Calculation Preview
Full download access to any calculation is available to users with a paid or awarded subscription (XLC Pro).
Subscriptions are free to contributors to the site, alternatively they can be purchased.
Click here for information on subscriptions.
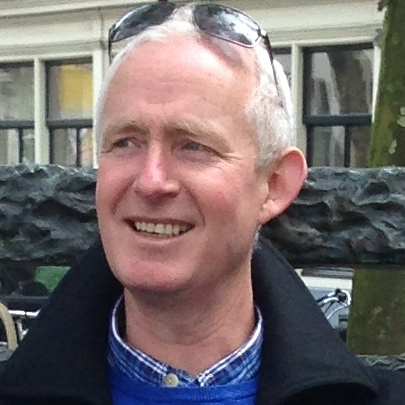