Construction Safety Inspection Checklist
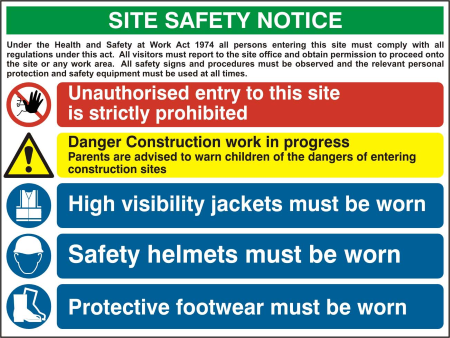
Description
A - Jobsite General
1. Posters and safety signs/warnings?
2. Safety meetings held periodically?
3. First aid kit available and adequately stocked?
4. Job related safety training completed?
5. Accident reporting procedure established?
6. Substance abuse policy in place?
7. Injury records being kept?
8. Emergency telephone numbers posted?
9. Traffic routes identified?
B - Housekeeping and Sanitation
1. General neatness of work area(s)?
2. Regular disposal of waste and trash?
3. Procedures to handle hazardous waste?
4. Passageways and walkways clear?
5. Adequate lighting?
6. Waste containers provided and used?
7. Sanitary facilities adequate and clean?
8. Adequate potable water supply?
9. Adequate drinking cups?
10. Nails, boards, debris removed?
11. Eye flushing facilities available?
12. Emergency showers available?
C - Construction Area - Secured Access/After Hours
1. Warning signs in place?
2. Open ditches protected?
3. Drop-offs protected?
4. Ladders lowered?
5. Hazard lights utilized?
6. Equipment secured?
7. Utility ditches flagged or barricaded?
D - Hazard Communication
1. Written program?
2. Employees trained?
3. MSDS's on file and available?
4. Control and disposal measure(s) established?
5. Material properly stored and labeled?
6. Log of all chemicals on site available?
7. Labels legible?
E - Fire Prevention
1. Adequate number and type of fire extinguisher(s) available?
2. Fire prevention/extinguisher training accomplished?
3. Fire extinguisher inspections accomplished (monthly/periodically)?
4. Phone number of fire department posted?
5. Fire extinguisher(s) provided on appropriate equipment?
6. Are flammable liquids in approved containers and correctly labeled?
7. Are flammable liquids properly stored?
8. Fire alarm available/fire evacuation plan established?
9. Fuel supplies protected from accidental impact?
-
Fire training given to appropriate personnel?
-
Is equipment shut down prior to refueling?
-
Is equipment properly grounded to fuel trucks before refueling
-
"No smoking" signs posted and enforced?
-
Hydrants clear, access to public thoroughfare open?
F - Flammable Liquids/Materials
1. Empty containers removed?
2. Only approved containers being used?
3. Containers stored in approved and appropriate area(s)?
4. Outside storage bermed for containment?
5. Storage tanks properly grounded, bonded & pressure relief provided?
6. Cylinders stored/secured in upright position?
G - Electrical
1. Electrical devices have current inspection and coding?
2. Electrical equipment properly maintained?
3. Equipment properly grounded?
4. Assured equipment grounding program established?
5. GFCI used and tested where required?
6. Fuses provided?
7. Electrical dangers posted?
8. Proper fire extinguisher(s) provided?
9. Are terminal boxes equipped with required covers (cover used)?
- Are circuits labeled in terminal boxes?
H - Personal Protective Equipment
1. Hazard evaluation accomplished and certified?
2. Protective equipment adequate for exposure?
3. Employees issued PPE where needed?
4. Is PPE being used?
5. Employees trained in the use of PPE?
6. Are inspections being accomplished periodically/before and after use?
7. Adequate maintenance and sanitary storage available/utilized?
8. Adequate fall protection provided?
9. Eye protection?
-
Face protection (glasses, goggles, shields)?
-
Hearing protection?
-
Respirators and masks?
-
Respirators used for harmful dust, asbestos, sand blasting, welding (lead, paint and galvanized zinc or cadmium)?
-
Head protection?
-
Hand and foot protection?
-
Physicals accomplished as required?
I - Hand Tools
1. Proper tool used for the job?
2. Handles free of cracks and attached to tool properly?
3. Inspections and proper maintenance accomplished prior to use?
4. Neatly stored, safely carried?
J - Power Tools
1. Good housekeeping where tools are used?
2. Inspections and proper maintenance accomplished?
3. Tools grounded properly or double insulated?
4. Guards in place and used correctly?
5. Damaged or malfunctioning tools tagged out until repaired or replaced?
6. Local laws and ordinance compliance?
7. All operators qualified?
8. Tools protected from unauthorized use?
9. Competent instruction and supervision?
- Cords included in electrical inspection?
K - Ladders
1. Ladders inspected and in good condition?
2. Ladders used properly for type of exposure?
3. Ladders secured to prevent slipping, sliding, or falling?
4. Do siderails extend 36" above top of landing?
5. Are ladders spliced?
6. Rungs or cleats not over 12" on center?
7. Proper maintenance and storage?
8. Are ladders painted?
9. Do fixed ladders in excess of 20 feet have fall protection?
10. Are aluminim ladders of sufficient strength for the task?
L - Scaffolds
1. Erection properly supervised?
2. All structural members free from defects and meet safety factor?
3. Are all connections secure?
4. Are scaffolds erected on solid footing?
5. Is scaffold tied to structure?
6. Are working areas free of dirt, debris, snow, ice, grease, etc.?
7. Are workers protected from falling objects?
8. Is scaffold plumb and square, with cross-bracing?
9. Are guard rails, intermediate rails, and toeboards in place?
-
Are ropes and cables in good condition?
-
Fall protection available and in use?
M - Excavation and Shoring
1. Are holes, trenches, and cuts over 5 feet deep shored, sloped or trench boxes used?
2. Operation supervised by competent person?
3. Spoil banks at least 2 feet from edges of cut?
4. Ladders placed to ensure no greater than 25 feet of lateral travel by worker?
5. Ladder properly secured?
6. Are adjacent structures properly shored?
7. Is shoring and sheathing correct for soil and depth?
8. Are roads and sidewalks supported and protected?
9. Excavation barricaded and lighting provided?
10. Are equipment ramps adequate?
11. Have underground utility installations been identified?
12. Registered professional engineer design/approval accomplished?
13. Confined space entry permit required plan established?
14. Are daily inspections completed by a competent person?
N - Tunneling
1. Testing of atmosphere accomplished?
2. Adequate ventilation?
3. Electrical approved for hazardous locations?
4. Adequate fire prevention?
5. Rescue plan?
6. Confined space entry permit program?
O - Hoists, Cranes and Derricks
1. Are annual inspections completed?
2. Are operators properly tested and physical exams current?
3. Are daily inspections completed by operators?
4. Outriggers used?
5. Power lines deactivated, removed, or warning signs posted warning of at least 10 foot clearance from overhead power lines (voltages 50,000 volts or below)?
6. Hoists designed by a competent professional engineer?
7. Proper loading for capacity at lifting radius?
8. Operation in accordance with manufacturer's instruction?
9. Competent person inspecting crane?
10. Equipment properly lubricated and maintained?
11. Load testing accomplished?
12. Signalmen where needed?
13. Alarms working and audible?
P - Heavy Equipment
1. Regular inspection and maintenance?
2. Seat belts provided and used in equipment with ROPS?
3. Backup alarms working and audible?
4. Slow moving vehicle emblem attached to rear of equipment operating at less than 25 mph?
5. No employees riding equipment without proper seating?
6. Lights, brakes, warning signals operative?
7. Wheels chocked when necessary?
8. Haul roads well maintained and laid out properly?
9. Equipment properly secured when not in use?
-
Noise arresters used?
-
Spark arresters used as necessary?
Q - Motor Vehicles
1. Regular inspection and maintenance?
2. Qualified operators?
3. Local and state laws observed?
4. Brakes, lights, warning devices operative?
5. Weight limits and load stress controlled?
6. Personnel carried in correct manner?
7. All glass in good condition?
8. Backup signals provided?
9. Fire extinguisher(s) installed?
-
Seat belts worn?
-
Tie down straps or chains inspected?
-
Are all vehicles checked at the beginning of each shift?
R - Garages and Repair Shops
1. Fire hazards controlled?
2. Oily rag containers used and emptied daily?
3. Good housekeeping?
4. Adequate lighting?
5. Adequate ventilation?
6. Are fuels and lubricants in proper containers?
7. Are fire extinguisher(s) provided, proper type and rating?
8. Ample absorbent materials available and in use?
S.Barricades
1. Floor openings planked over or barricaded?
2. Roadways and sidewalks protected?
3. Adequate lighting provided?
4. Barricades or covers installed (shafts, wall openings, stairways, stairwells, trenches, outriggers, etc.)?
T - Handling and Storage of Materials
1. Materials properly stored or stacked?
2. Are shelves, racks, and overhead storage load rated?
3. Are passageways clear?
4. Sufficient employees to do the job?
5. Lifting correctly?
6. Materials protected from weather?
7. Employees protected from falling into hoppers and bins?
8. Is dust protection used?
9. Correct type of fire extinguisher(s) and other fire protection available?
10. Traffic controlled through the storage area?
11. Rigging inspected prior to use?
12. Competent person responsible?
U - Demolition
1. Engineering survey in writing?
2. Are material chutes provided and used?
3. Are operations planned ahead?
4. Is there shoring of adjacent structures?
5. Utilities shut off?
6. Hazardous materials/chemicals removed from any pipes,
tanks, or equipment?
7. Chutes provided for disposing of material above 20 feet?
V - Blasting
1. Contractor qualifications and credentials checked?
2. Explosive inventory completed and accounted for at all times?
3. Stray electrical currents checked?
4. Blasting mats used when required?
5. All signs, warning signals, and protective equipment in place?
6. Non-essentials removed from area?
7. Radio transmissions limited?
8. Procedures for handling misfires in place?
9. Explosives properly stored?
10. Is black powder prohibited?
11. Experienced and trained personnel handling explosives?
12. Detonators tested before each shot?
13. Area inspection after each shot?
14. Proper disposal of wrappings, waste, and scrap?
15. Operations suspended during electrical storms or when lightning is within 10 miles?
16. Explosives and related materials properly stored?
17. All blasting operations conducted between sun-up and sun-down
W - Welding and Cutting
1. Are operators qualified?
2. Screens and shields in place?
3. Are oxygen and acetylene stored properly?
4. Are bottles not in use secured with caps in place?
5. Proper eye protection and PPE used?
6. Fire extinguisher located near operations?
7. "Hot work" permit completed and posted in areas requiring such permit?
8. Are valves shut-off and regulators backed off each night?
9. Flashback arresters placed on hoses (O2 and fuel gas)?
10. Electrical equipment grounded?
11. Area inspected for fire hazards?
12. Gas lines and power cables protected and in good condition?
13. Proper ventilation?
14. Welding permit program?
X - Steel Erection
1. Safety nets or planked floors?
2. Hard hats, safety shoes, gloves and other PPE used?
3. Taglines for controlling loads?
4. Fire hazards covered and barricaded?
5. Floor openings covered and barricaded?
6. Hoisting apparatus checked?
7. Adequate fall protection?
8. Christmas treeing used correctly?
Y - Concrete Construction
1. Forms properly installed and braced?
2. Adequate shoring, plumbed, and crossbraced?
3. Proper curing period and procedures used?
4. Adequate PPE?
5. Caps on rebar?
6. Automatic shutoff on power operated trowels?
7. Nails and stripped form material removed from area?
Z - Masonry
1. Proper scaffolding?
2. Masonry saws properly equipped, dust protection provided?
3. Safe hoisting equipment?
4. Are limited access zones established as required?
AA - Highway Construction
1. Competent flagmen properly dressed, trained, and posted?
2. Adequate warning signs and markers?
3. Equipment not blocking right-of-way?
4. Traffic control through construction site?
5. Adequate marking and maintenance of detours?
6. Dust control used?
7. Adequate lighting?
8. Are barricades erected with correct directional stripes?
AB - Asbestos
1. If unexpected presence detected, is stop work procedure established?
2. Owner been notified?
3. Area secured?
AC - Work Permits
1. Safe work permit procedures followed?
2. "Hot work" permit procedures followed?
3. Excavation permit procedures followed?
4. Control of hazardous energy (lockout/tagout) procedures being used?
5. Confined space entry permit procedures followed?
6. Are emergency rescue plans established and available?
Note: This construction safety inspection checklist is not designed to supersede existing safety inspection checklists, rather it should be used only as a general guideline. You are encouraged to customize this general guideline to accommodate your specific operations.
Calculation Reference
Construction Site Safety
Health Safety and Environment
Safety Policies and Procedures
Calculation Preview
Full download access to any calculation is available to users with a paid or awarded subscription (XLC Pro).
Subscriptions are free to contributors to the site, alternatively they can be purchased.
Click here for information on subscriptions.
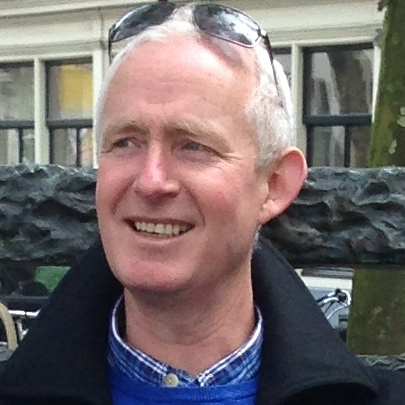