Fillet Weld Static Strength.xls
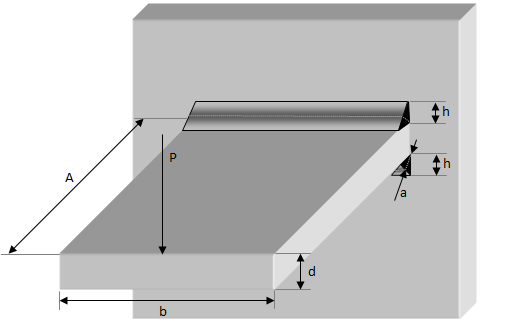
Description
Fillet weld generally fails due to shear stresses in the weld throat. For typical construction materials allowable shear stresses are about 2/3 of the allowable tensile stress. Compare with butt weld calculation.
To calculate the weld strength of a simple plate connected with two fillet welds, follow these steps:
- Determine the geometry and material properties of the fillet welds:
- Leg length (z): The distance from the root to the toe of the weld.
- Throat thickness (a): The minimum distance from the root of the weld to its face, which is equal to the leg length (z) multiplied by the sine of the included angle (usually 45 degrees for fillet welds). So, a = z * sin(45°) = z * 0.707.
- Length of each weld (L1 and L2): The length of the two fillet welds.
-
Determine the weld material's design strength (f_wd). This can be calculated using the ultimate tensile strength (f_u) or yield strength (f_y) of the weld material, depending on the design code being followed (such as AISC, Eurocode 3, or BS 5950). Divide the material strength by the appropriate partial safety factor (e.g., 1.25 for Eurocode 3 or BS 5950).
-
Calculate the design shear capacity (P_v1 and P_v2) of each fillet weld:
P_v1 = C * f_wd * a * L1 P_v2 = C * f_wd * a * L2
where C is a constant factor that depends on the design code (0.5 for Eurocode 3, or 1/√3 for BS 5950).
- Calculate the total design shear capacity (P_v) of the connection:
P_v = P_v1 + P_v2
The calculated weld strength (P_v) should be checked against the applied loads on the connection to ensure that the welds have adequate capacity to resist the forces. It's important to consult the relevant design codes for specific requirements and limitations when designing fillet weld connections.
Calculation Preview
Full download access to any calculation is available to users with a paid or awarded subscription (XLC Pro).
Subscriptions are free to contributors to the site, alternatively they can be purchased.
Click here for information on subscriptions.