Calculation of Pump Sizing

Description
Calculation of Pump Sizing & Curve Pump sizing is an important process to ensure that a pump can efficiently meet the required flow and pressure needs of a system. The basic steps involved in calculating pump sizing include:
Determine the Required Flow Rate (Q) • The flow rate is the amount of fluid that must be moved by the pump per unit of time, usually expressed in gallons per minute (GPM) or liters per second (L/s). • Consider the application requirements, including pipe sizes, equipment, and the desired throughput.
Determine the Total Head (H) • The total head is the energy the pump needs to impart to the fluid to move it through the system. It is usually measured in feet or meters and can be broken down into: o Static Head: The vertical distance the fluid needs to be lifted. o Friction Head: The loss of pressure due to friction in the pipes, valves, fittings, and other components. o Velocity Head: Energy due to the velocity of the fluid (usually minimal in many applications). The total head is the sum of all these components. Formula for Head (H): H=Hstatic+Hfriction+Hvelocity
Calculate Pump Power Requirement • The pump power is the energy required to achieve the specified flow and head. This is often calculated using the formula: P= Q×H×ρ×g Efficiency
Where: • PP = Pump power (W or HP) • QQ = Flow rate (m³/s or GPM) • HH = Total head (m or ft) • ρ\rho = Density of the fluid (kg/m³ or lb/ft³) • gg = Acceleration due to gravity (9.81 m/s² or 32.2 ft/s²) • Efficiency is the efficiency of the pump (typically between 50% and 90%). 4. Select a Pump Based on Manufacturer Curves • Pump manufacturers provide performance curves that relate flow to head for different types of pumps. The curve shows the flow rate for a given head, and you can use it to select a pump that meets the required flow and head. 5. Account for System Conditions and Variations • Conditions like temperature, pressure, and fluid characteristics can affect pump performance. Adjust for these variables during sizing to ensure reliability under real-world conditions. 6. Check for NPSH (Net Positive Suction Head) • Ensure that the pump is capable of operating without cavitation. The NPSH required by the pump should be lower than the NPSH available in the system. 7. Final Pump Selection • Based on the above calculations, select a pump that meets the required flow, head, and other operating conditions. Ensure that the pump operates within the best efficiency range (BEP).
Pump Sizing Calculation - Engineering Principles
A pump sizing calculation is fundamentally about determining the appropriate pump specifications to meet a specific fluid transfer requirement. The key engineering principles involved include:
Fluid Mechanics Fundamentals
The calculation likely applies Bernoulli's equation and continuity principles to analyze how fluid moves through a system. This relates pressure, velocity, and elevation changes throughout the piping system.
Head Calculations
Pumps are typically sized based on the "head" they need to overcome:
Static head: The vertical distance the fluid needs to be lifted
Friction head: The resistance to flow due to pipe friction and fittings
Velocity head: Related to the kinetic energy of the moving fluid
Pressure head: Additional pressure requirements at the destination
Flow Rate Requirements
The calculation would determine the required flow rate based on the system needs, usually expressed in units like gallons per minute (GPM) or cubic meters per hour (m³/h).
System Curve Analysis
This involves analyzing how the system resistance changes with flow rate, creating what's called a "system curve." As flow increases, resistance typically increases exponentially.
Pump Selection
Once the required head and flow rate are established, the calculation would help identify a pump that can operate efficiently at those conditions, often by matching the system curve with manufacturer pump curves.
Efficiency Considerations
The calculation likely evaluates energy efficiency by analyzing:
Pump efficiency at the operating point
Motor sizing requirements
Net Positive Suction Head (NPSH) calculations to prevent cavitation
Power Requirements
The calculation would determine the power needed to operate the pump, usually in horsepower or kilowatts, based on flow rate, head, and efficiency factors.
Pump Sizing Calculation - Worked Example
Scenario
Water needs to be pumped from a storage tank to a rooftop tank in a building
Vertical height (elevation difference): 30 meters
Horizontal pipe length: 150 meters
Pipe diameter: 100 mm (4 inches)
Required flow rate: 40 cubic meters per hour (m³/h)
Water temperature: 20°C
Step 1: Calculate Static Head
Static head is the vertical distance the water must be lifted:
Static head = 30 meters
Step 2: Calculate Friction Head Loss
Using the Darcy-Weisbach equation and assuming a pipe roughness factor:
Flow velocity = 1.41 m/s (based on 40 m³/h through a 100 mm pipe)
Friction factor = 0.02 (depends on pipe material and Reynolds number)
Friction head loss in straight pipe = 6.8 meters
Additional loss from fittings (elbows, valves, etc.) = 3.2 meters
Total friction head loss = 10 meters
Step 3: Calculate Total Dynamic Head (TDH)
TDH = Static head + Friction head loss
TDH = 30 + 10 = 40 meters
Step 4: Calculate Required Pump Power
Power (kW) = (ρ × g × Q × H) ÷ (η × 1000)
Where:
ρ = density of water (1000 kg/m³)
g = acceleration due to gravity (9.81 m/s²)
Q = flow rate (0.011 m³/s)
H = total head (40 m)
η = pump efficiency (assumed 70%)
Power = (1000 × 9.81 × 0.011 × 40) ÷ (0.7 × 1000) = 6.2 kW
Step 5: Check NPSH (Net Positive Suction Head)
Atmospheric pressure (at sea level) = 10.33 meters of water
Vapor pressure of water at 20°C = 0.24 meters of water
Static suction lift = 2 meters (assumed)
Friction losses in suction pipe = 0.5 meters
NPSHa = 10.33 - 0.24 - 2 - 0.5 = 7.59 meters
Required NPSHr (from pump specifications) = 3 meters (assumed)
Since NPSHa > NPSHr, cavitation should not occur
Step 6: Select a Pump
Based on these calculations, we need a pump that can:
Deliver 40 m³/h flow rate
Provide 40 meters of head
Require approximately 6.2 kW of power
Operate efficiently at these conditions
Have an NPSHr less than 7.59 meters
Step 7: Operating Cost Estimation
Annual electricity consumption = 6.2 kW × operating hours per year
At 12 hours/day operation: 6.2 kW × 4380 hours = 27,156 kWh
At $0.15/kWh: Annual operating cost = $4,073
This example demonstrates how engineering principles like fluid mechanics, hydraulics, and energy efficiency come together in a practical pump sizing calculation. The final pump selection would involve reviewing manufacturer data sheets to find a pump that meets these requirements while operating near its best efficiency point.
Calculation Preview
Full download access to any calculation is available to users with a paid or awarded subscription (XLC Pro).
Subscriptions are free to contributors to the site, alternatively they can be purchased.
Click here for information on subscriptions.
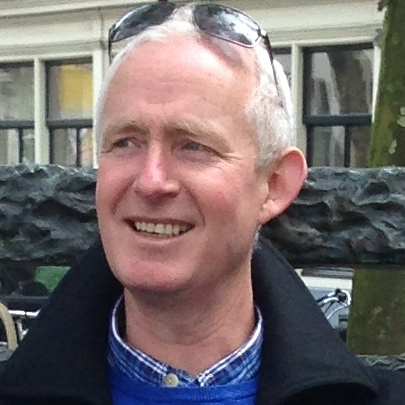