Bend Allowance
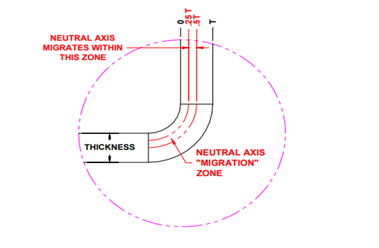
Description
Here are the key points about bend allowance and sheet metal forming:
- Bend allowance describes how much extra material is needed between two panels to accommodate a bend. Determining bend allowance is called bend development.
- The neutral axis is the length that does not change during bending. Material inside the neutral axis compresses, outside stretches.
- The neutral axis position (K-factor) depends on geometry - tight bends have axis near inside, gradual bends have axis near center.
- Common k-factors: wrapped hem (.29), machine bend with set (.33), no set (.38), V-bend (.42), rotary (.43), gradual bend (.50).
- Bend allowance formula relates radius, angle, thickness, and k-factor to calculate length. Can use radians or convert degrees.
- Special cases: Z-bends can elongate middle panel, wrapped hems thin and vary, shallow bends blend neutral axis, gussets drive material.
- Key principles: neutral axis migrates based on compression/tension, axis limits are ~.25-.50 thickness, allowances depend on specific tooling and geometry. Test pieces are recommended to validate.
In summary, bend allowance compensates for material compression and stretch during bending. The neutral axis position and allowance formulas help estimate the extra length needed. Allowances vary based on tooling and geometry, so testing is advised.
Calculation Preview
Full download access to any calculation is available to users with a paid or awarded subscription (XLC Pro).
Subscriptions are free to contributors to the site, alternatively they can be purchased.
Click here for information on subscriptions.
Comments: 1
×
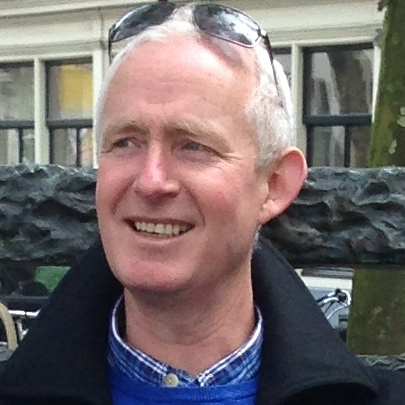
johndoyle-admin
1 year ago
A useful debut calculation! Thanks for sharing! I have awarded a three month XLC Pro subscription by way of thanks.